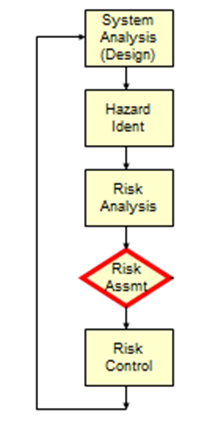
The air show industry has talked at length about Safety Management Systems (SMS) and how ICAS as an industry needs to develop a functional SMS. But, as the aviation industry and, more importantly, the air show community get a better understanding of the philosophy and implementation of a real SMS, it also becomes clearer that the goal of and expectations for an air show SMS need to be modified.
Since ICAS began its initiative to change the culture of air show safety in 2008, the industry has continually improved and expanded its understanding of what constitutes a working SMS. There are certain core pillars that remain constant in any effective SMS: policy, safety risk management, safety assurance and safety promotion. As ICAS continues to improve its capacity to introduce SMS to the air show industry, it is useful for all air show professionals to develop a working knowledge of risk management as a tool in improving the level of safety for individual air shows, performers and the larger air show industry.
Safety risk management (SRM), as defined by the International Civil Aviation Organization (ICAO) Safety Management Manual (SMM), is “…a generic term that encompasses the assessment and mitigation of the safety risks of the consequences of hazards that threaten the capabilities of an organization, to a level as low as reasonably practicable.” Simply put, the SRM process is an examination of why a system works, anticipation of what happens when it does not work, and a common understanding of what outcomes are universally agreed to be unacceptable. The SRM process can be used in nearly every aspect of the air show industry. It should be used when a performer adds a new maneuver to his/her routine, when a new performer develops their first routine, when an event organizer develops a site layout, or when a regulatory inspector requires a change to the location of the crash fire rescue.
SRM should be used during any initial system or task analysis, for any changes to existing systems, procedures or equipment, and whenever a new hazard is discovered in day to day operations. The use of the SRM process should become a universal constant across all fields of the air show industry.
SRM is a flow of actions that begins with analyzing a specific system or task. During this analysis, one identifies potential hazards. A hazard is a condition or object with the potential to cause injuries, damage or a reduction of the ability to perform a prescribed function. Each hazard to the system or task must be identified in a systematic manner. There are many external methods to identify hazards (system and task analysis, reporting programs and operational data trend analysis); however, because air show professionals have vast amounts of operational-specific knowledge, internal methods of hazard identification are often best in our industry. Some examples of internal hazard identification tools are:
- Comparative Safety Assessment. Assesses and compares the safety risk of selective alternatives.
- Preliminary Hazard List. Provides an initial overview of the possible hazards in the overall flow of a system.
- Bow-Tie Model. Provides a pictorial understanding of the possible causes and effects of a hazard.
- Operations Analysis Tool. Provides an itemized sequence of events or a flow diagram depicting the major events of an operation.
- “What If” Process Tool. Commonly known as table top exercises, this allows for the visualization of hazards.
Once hazards are identified and confirmed, a risk analysis is performed to assess its potential for harm. Measuring the probability and the severity of possible consequences of a hazard allows for an assessment of each outcome. This risk assessment is performed by determining if the assessed risks are acceptable and within an organization’s safety criteria. If so, the risk is considered acceptable. However, if the risk is deemed unacceptable, it is necessary to take action to reduce the risk to an acceptable level.
One simple example of how a performer might put SRM to appropriate use: Consider an air show performer seeking to modify his aircraft by switching from a sturdy, heavy fuel hose to a lightweight, composite fuel hose. The performer would begin a system analysis by consulting a mechanic, the composite hose manufacturer and other pilots that have used the composite hose to determine any known or possible failures with the hose. The performer then determines that there are three possible hazards that come with the installation of a new fuel hose: hazards A, B and C. Hazard A has an extremely low probability of occurring, but would be catastrophic if it did. Hazard B has a moderate probability of occurring, and would be a major problem, but not necessarily catastrophic. Hazard C has a frequent probability of occurring, and has next to no effect on safety.
The performer would then assess each of the risks posed by the hazards and make a decision. The performer might determine that, since the risks associated with Hazard A are so remote, there would be no benefit to mitigation, and, therefore, categorize Hazard A as an acceptable risk. The performer would likely categorize the risk associated with Hazard C in a similar manner due to the negligible effect on safety despite the likelihood of frequent occurrence. The performer might determine, however, that Hazard B represents an unacceptable risk due to the combination of high risk and probable occurrence. The performer would then take action to reduce the probability or severity of Hazard B. To complete the SRM process, the performer would then subject his solution to Hazard B to the SRM process to see if the control he plans to enact would have any secondary hazards.
Although the example used above relates directly to a performer, the SRM process is just as useful to non-performers. Event organizers and virtually all support service providers must regularly assess risks present in their part of the air show environment. Imagine that you are the director of the fictional Acton Air Show. Being a wise air show professional, you know that since your show is in May, you will have a high probability for inclement weather. You have several large tents and plenty of hangar space for temporary coverage in the event of a thunderstorm. On the morning of your show, the weatherman tells you that you are going to have a sunny day except between 2:00 and 3:00 in the afternoon when a fast squall line will pass through. The weatherman warns you that the storm has been producing massive amounts of lightning strikes.
As the show’s director, you would work this possible hazard through the SRM process. You would first determine all hazards associated with this squall line. After determining that high winds, lightning and rain are hazards, you would then perform a risk analysis on each hazard. High winds could very possibly blow tents or unsecured structures down, causing injury or worse. Lightning possibly striking a spectator would cause injury or worse. Rain would definitely cause an acceptable level of discomfort to the spectators, but would not directly cause major injury or loss. The next step in the SRM process would be to make a risk assessment, or a decision, on the acceptability of each risk. High winds would be acceptable if you mitigate the risk of the tents and structures being blown down by tying down the structures. Lightning strikes would be unacceptable under the existing circumstances, so you would be sure you schedule a concert in a covered hangar to keep your spectators inside and away from the unacceptable risk of lightning. Rain, however, would have such a low impact on the spectators that it would be classified as acceptable. Now that you have successfully mitigated all risks as low as possible, you will finish the process by analyzing your mitigation strategy to look for possible latent hazards. To make genuine progress on improving safety in our business, we must all be willing to conduct the business of safety differently than we have in the past. Using the SRM process represents a straightforward, logical and comparatively easy way to make forward progress in that area. This year, demonstrate your commitment to putting safety first by putting SRM to use in your air show business.